Применение ультразвуковых
толщиномеров покрытий
David Beamish, DeFelsko Corporation
(После проверки в публикациях: "Finishing
Today", 02'2008 г.;
"Materials Performance
Magazine", 09'2004 г. ;
"Quality Digest Magazine", 10'2004 г.)
Толщиномеры
покрытий, применяющие методику измерения с помощью ультразвука. Они
подтверждают или заменяют разрушающие методы для измерения толщины покрытий на
древесине и изделиях из древесины.
Покрытия
выполняют множество функций. Некоторые предназначены для реставрации, защиты,
водонепроницаемости и украшения структуры дерева. Другие специально разработаны
для заливки и заполнения пор и для обеспечения эстетически привлекательной
текстуры поверхности. Проникающие отделочные покрытия впитываются в древесину и
затвердевают, образуя прочный, не отслаивающийся защитный барьер.
Зачем нужно измерять толщину?
Покрытия
разрабатываются для выполнения предназначенных им функций и лучше всего, когда
они наносятся в узком, установленным производителем диапазоне толщин. Например,
лаки тверже, чем другие покрытия, и для предотвращения растрескивания и других
повреждений отделки толщина их сухой пленки не должна превышать 5 мил (127
микрон). Нитроцеллюлозный лак обычно должен наноситься толщиной мене 3 мил (76
микрон). Для достижения желаемого эффекта отделки – получения декоративной
сетки трещин основным является постоянная толщина при нанесении основных
лаковых покрытий и грунтов с трещинами.
На
древесно-волокнистой плите средней плотности (ДВПСП), как правило, наносят
порошковое покрытие толщиной от 3 до 9 мил (76 – 230 микрон). Обычно, чем толще
покрытие, тем выше прочность отделки. Заводские технические условия часто
требуют установленного допуска ± 1 мил (25 микрон). Этот уровень качества
нельзя определить, только посмотрев на него.
Существуют и
другие преимущества в точном измерении толщины отделочных покрытий. Когда
компаниям не удается проверить и подтвердить качество покрытия входящих
материалов, они тратят деньги на переделки. При контроле технологии напыления
операторами, они гарантируют, что покрытие наносится в соответствии с
рекомендациями производителей. Кроме того, нанесение чрезмерной толщины пленки
может радикально понизить общую эффективность. В конечном счете ,
систематический контроль может снизить количество внутренних переделок и
возвратов покупателей из-за дефектов отделки.
Как лучше контролировать?
Контроль толщины
покрытий на металле – это обычное явление для контроля и проверки качества.
Когда основным металлом является углеродистая сталь, применяется магнитный
метод. Вихретоковые приборы применяются для других металлов, таких как медь и
алюминий.
В связи с
тем, что эти приборы не могут измерять толщину отделочных покрытий на
древесине, применяемые альтернативные методы включают:
- Оптическое исследование
поперечного сечения (разрезание покрытой детали и просмотр разреза под
микроскопом)
- Измерение высоты (измерение
микрометром до и после покрытия)
- Гравиметрическое исследование
(измерение массы и зоны покрытия для расчета толщины)
- Погружение толщиномера мокрой
пленки в мокрую краску и расчет толщины сухой пленки, используя процент
сухого остатка в объеме.
- Подстановка (помещение
стального образца рядом с деревянной деталью и нанесение покрытия на них
одновременно)
Эти методы
контроля требуют больших затрат времени, трудны для выполнения и являются
предметом для интерпретации оператора и других ошибок измерения. Специалисты по
нанесению покрытий находят эти методы непрактичными. Для получения
статистически представительного образца несколько изделий из дерева из партии
должны быть списаны, как часть процесса разрушающего контроля.
С появлением
ультразвуковых приборов многие отделочники переключились на неразрушающий
контроль.
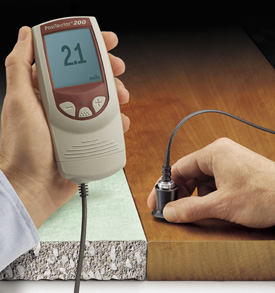
|
Рис.1 Ультразвуковой
толщиномер покрытий PosiTector 200
|
Ультразвуковой прорыв
Профессионалы
качества уже хорошо знакомы с различными аспектами ультразвукового контроля, в
котором для проведения контроля и выполнения измерений применяется
звуковая энергия высокой частоты. Ультразвуковой контроль может выявлять и
оценивать трещины в металле, измерять размеры, устанавливать характеристики
материала и т.д.
Измерение
толщины стенки вероятно является наиболее известным и простым видом
ультразвукового контроля. Прецизионные ультразвуковые толщиномеры стенки дают
возможность быстрого измерения толщины объектов при одностороннем доступе.
Однако для измерения покрытия эти приборы не являются идеальными. У них нет
достаточной чувствительности для измерения толщины акриловых шпатлевок,
заводских грунтовок, лаков, УФ отделочных покрытий, порошковых покрытий и
других материалов, применяемых по древесине.
Первый
портативный прибор, предназначенный специально для измерения толщины покрытия,
появился на рынке 14 лет назад, и сейчас представлено четвертое поколение. В
нем применяется совмещенный преобразователь и усовершенствованная цифровая
аппаратура для отфильтровывания и усиления оцифрованных эхосигналов.
Сегодняшние портативные ультразвуковые толщиномеры покрытий просты в работе,
допустимы по средствам и достоверны (Рисунок 1).
Метод измерения звука
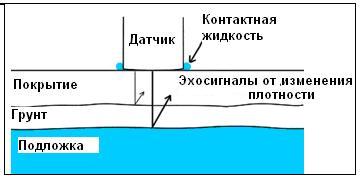
|
Рис. 2 Ультразвуковые
колебания отражаются от границ покрытий
|
Ультразвуковой
контроль выполняется, посылая ультразвуковые колебания с помощью датчика
(преобразователя) в покрытие через нанесенную на поверхность контактную
жидкость.
Колебание
проходит через покрытие до столкновения с материалом с отличающимся
механическими свойствами, как правило, с подложкой, но может быть с другим
слоем покрытия. Колебание частично отражается от этой границы, проходит назад в
преобразователь. Тем временем часть посланного колебания продолжает двигаться
за пределами этой границы и испытывает дальнейшие отражения от любых границ
материалов, с которыми сталкивается (Рисунок 2).
Т.к.
потенциально может быть большое количество отраженных сигналов, для расчета
измерения толщины прибор выбирает максимальный или «наиболее сильный»
отраженный сигнал. Приборы, которые измеряют отдельные слои в многослойной
системе покрытия, также предпочитают наиболее сильные отраженные сигналы.
Пользователь просто вводит количество слоев для измерения, говорит три, и
прибор измеряет три наиболее сильных отраженных сигнала. Прибор игнорирует
более слабые отраженные сигналы от дефектов в покрытии и от подложки.
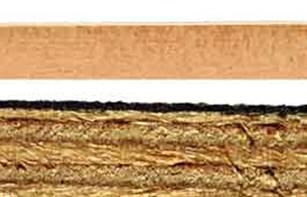
|
Рис. 3 Примеры
шероховатых зон покрытие/подложка
|
Точность измерения
Точность любого
ультразвукового измерения непосредственно соответствует скорости звука в
измеряемом отделочном покрытии. Т.к. ультразвуковые приборы измеряют время
прохождения ультразвукового импульса, они должны быть откалиброваны на
«скорость звука» в этом индивидуальном материале.
С
практической точки зрения, значения скорости звука материалов покрытий,
применяемых в деревообрабатывающей промышленности, сильно не отличаются.
Поэтому ультразвуковые толщиномеры покрытий, как правило, не требуют настройки
заводских установок калибровки.
Как покрытие стыкуется с подложкой
Фактором,
влияющим на точность и воспроизводимость ультразвукового измерения, является
состояние границ этих покрытий с подложкой из древесины. На рисунке 3 показаны
два примера древесины с покрытием.
Эти фотографии, сделанные с более высоким разрешением, чем допускают
большинство разрушающих испытаний, ясно показывают границу между отделочным
покрытием и древесиной. Сверху отделочное покрытие может выглядеть гладким, но
толщина может быть противоречивой. Древесные подложки часто шероховаты с
различной степенью шероховатости поверхности и проникания грунта. Такая
пористость и шероховатость могут способствовать адгезии, но из-за них
возрастает трудность достижения любыми средствами воспроизводимых измерений
толщины.
Ультразвуковые
приборы усредняют небольшие неравномерности, чтобы дать достоверный результат.
На очень грубых поверхностях или подложках, где отдельные показания не могут
выглядеть воспроизводимыми, сравнение серий усредненных результатов часто
обеспечивает приемлемую воспроизводимость.
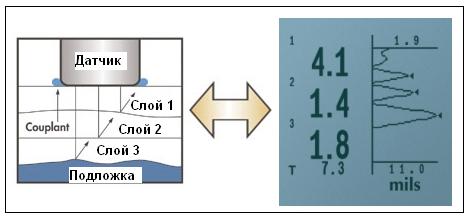
|
Рис. 4 Некоторые приборы измеряют отдельные слои в
многослойной системе покрытия.
В этом примере: слой 1 – толщиной 4,1 мила, слой 2 –
толщиной 1,4 мила, слой 3 – толщиной 1,8 мила. Суммарная толщина - 7,3 мила.
На графическом ЖКД изображены три «пика», означающие три границы материалов.
|
Обеспечение надлежащего звучания
Ультразвуковой
контроль приносит особую пользу в деревообрабатывающей промышленности. Производители
мебели, настила пола и музыкальных инструментов часто наносят несколько слоев
лака и подобных отделочных материалов. Некоторые процессы требуют возможности
определения толщины отдельных слоев или серии слоев. Когда нанесена
несоответствующая толщина, слой покрытия, который украшает и защищает,
например, гитару, может легко понизить ее звучание. Слишком большой слой
покрытия может ослабить акустический резонанс гитары, слишком маленький –
приведет к противоположному результату.
В настоящее
время для точного и неразрушающего измерения толщины лака на своих
дорого-стоящих изделиях производители музыкальных инструментов применяют
ультразвуковые приборы. В результате применения этой новой технологии они не
только снизили применение лака, они также в состоянии теперь получать
достоверные измерения без чрезмерного нарушения своего производственного
процесса. Нет необходимости списывать изделие из-за измерения толщины покрытия,
и можно легко измерить толщину на всей поверхности, чтобы гарантировать гладкое
равномерное покрытие. Благодаря возросшей возможности управления процессом
покрытия минимизируются переделки.
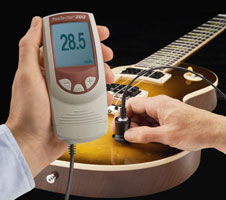
|
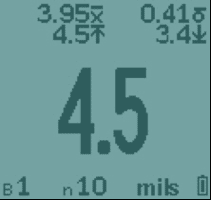
|
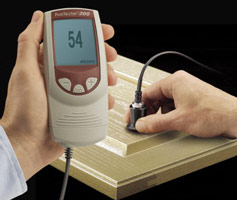
|
Рис. 5 Неразрушающее измерение толщины лака на древесине
гитар
|
Рис. 6 Некоторые приборы обеспечивают статический анализ.
В этом примере сделано 10 измерений.
На дисплее отображены: последнее измерение - 4,5 мила, среднее значение,
среднеквадратичное отклонение и максимальная/минимальная величины из 10
показаний.
|
Рис. 7 Прибор прост в работе, недорогой и надежный
|
Заключение
В настоящее
время ультразвуковое измерение толщины покрытия является общепринятой и
надежной практикой контроля, применяемой в деревообрабатывающей промышленности.
Стандартный метод контроля описан в ASTM D6132-04 «Стандартный метод контроля
для неразрушающего измерения толщины сухой пленки нанесенного органического
покрытия с использованием ультразвукового прибора» (2004, ASTM). Для
подтверждения калибровки прибора поставляются эталонные образцы толщины
эпоксидного покрытия с сертификацией, отвечающей требованиям национальных
организаций сертификации.
В настоящее
время неразрушающие измерения толщины могут проводиться на материалах, которые
ранее требовали разрушающих испытаний или лабораторного анализа. Эта новая
технология повышает последовательность и производительность в цехах отделки.
Возможно снижение стоимости в связи с:
- Минимизация затрат от покрытия
при применении управления толщиной наносимого покрытия
- Минимизация переделок и ремонта
вследствие непосредственной обратной связи с оператором и улучшения
управления процессом
- Устранение необходимости
разрушать и ремонтировать объекты при проведении разрушающих измерений
толщины покрытия.
Сегодня эти
приборы просты в работе, доступны по ценам и надежны. Источник: сайт ООО Панатест
|